鈦材的加工工藝方法分析
時(shí)間:2022-02-03 10:31:51 點(diǎn)擊:0次
鈦金屬物理性能優(yōu)質(zhì),而使用性能較弱,這就致使了其應(yīng)用前景看中但加工比較艱難這一分歧。文中根據(jù)剖析鈦金屬原材料的金屬材料加工性,融合很多年具體工作經(jīng)歷,在加工鈦合金刀具的采用、切削用量的明確、不一樣鉆削方式的特性、加工容量及加工常見問題等多個(gè)方面實(shí)現(xiàn)了討論,表明了自己對鈦金屬機(jī)械設(shè)備加工層面的個(gè)人見解和提議。
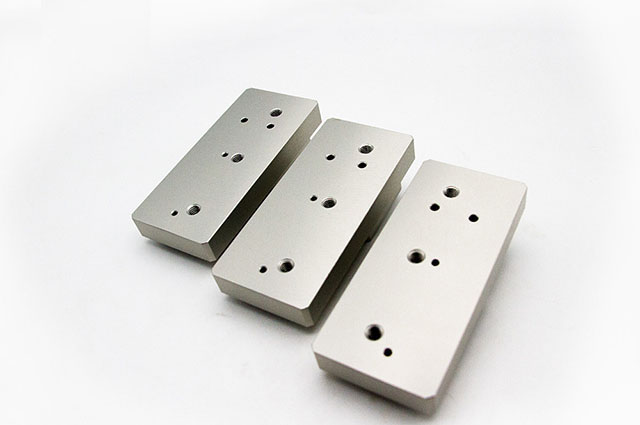
前言
鈦合金密度低、強(qiáng)度(抗壓強(qiáng)度/相對密度)高、耐腐蝕特性好、耐溫性高、延展性、可塑性、可鍛性均不錯(cuò),現(xiàn)階段在航天航空、車輛、醫(yī)藥學(xué)、文體用品及電解法工業(yè)生產(chǎn)等很多行業(yè)均已很多應(yīng)用鈦金屬。但傳熱性會差、強(qiáng)度高、彈性模具劣等特點(diǎn)也造成鈦金屬變成較難加工的金屬材質(zhì)。文中是對于其加工工藝特點(diǎn)匯總出的鈦金屬鉆削加工中的一些加工工藝對策。
鈦金屬原材料的具體優(yōu)勢
(1)鈦金屬抗壓強(qiáng)度高而相對密度?。?.4kg/dm3)、重量較輕,為一些大中型零部件緩解凈重給予了解決方法。
(2)熱強(qiáng)高朝。鈦金屬在400~500℃標(biāo)準(zhǔn)下仍能保持較高的抗壓強(qiáng)度,可以好的工作,而鋁合金的操作溫度只有在200℃下列。
(3)與不銹鋼板材對比鈦金屬原有的高耐腐蝕性可以節(jié)約飛機(jī)場日常運(yùn)作和維修保養(yǎng)的成本費(fèi)。
鈦金屬加工特點(diǎn)剖析
(1)傳熱系數(shù)低。TC4在200℃通信零件加工時(shí)導(dǎo)熱系數(shù)l=16.8W/m?℃,傳熱系數(shù)是0.036卡/公分?秒?℃,僅是鋼的1/4,鋁的1/13,銅的1/25。在鉆削加工全過程中排熱和制冷實(shí)際效果差,減少了數(shù)控刀片使用壽命。
(2)彈性模具低,零件已加工表層回彈力大,造成已加工表層與數(shù)控刀片的后刃口觸碰總面積擴(kuò)大,既危害零件規(guī)格精密度又減少了刀具耐用度。
(3)強(qiáng)度要素。強(qiáng)度值低的鈦金屬加工的時(shí)候會發(fā)粘,切削沾在數(shù)控刀片前刃口的鉆削刃周邊產(chǎn)生加工硬化,危害加工實(shí)際效果;強(qiáng)度偏高的鈦金屬加工時(shí)非常容易使數(shù)控刀片造成崩刃和浸蝕。這種特點(diǎn)造成鈦金屬金屬材料污泥負(fù)荷低,僅為鑄鐵件的1/4,加工時(shí)間較同規(guī)格鑄鐵件要看起來多。
(4)有機(jī)化學(xué)兩親性強(qiáng)。鈦不但可以與空氣中的主要成分氮、氧、一氧化碳等化學(xué)物質(zhì)產(chǎn)生化學(xué)變化,在鋁合金表層產(chǎn)生TiC及TiN硬底化層,并且在鉆削加工造成的高溫情況下還能與刀具材料起反映,減少了數(shù)控刀片的耐磨性能。
(5)鉆削全過程中的安全系數(shù)差。鈦歸屬于易燃性金屬材料,少量鉆削時(shí)加工中形成的高溫和火苗有可能造成鈦屑點(diǎn)燃。
鈦金屬加工加工工藝方式
(1)盡量應(yīng)用硬質(zhì)合金刀具,鎢鈷類硬質(zhì)合金刀具具備硬度高、傳熱性不錯(cuò)的特性,與鈦高溫下也不容易產(chǎn)生化學(xué)變化,合適用于加工鈦金屬。
(2)有效挑選數(shù)控刀片幾何圖形主要參數(shù)。為減少鉆削溫度,降低數(shù)控刀片粘接狀況,可適度減少數(shù)控刀片偏角,根據(jù)提升切削與前刃口的觸碰總面積來排熱;與此同時(shí)擴(kuò)大數(shù)控刀片前角,降低因已加工表層回彈力與數(shù)控刀片后刃口磨擦觸碰而造成數(shù)控刀片粘接、已加工表層精密度減少的狀況;尖刀宜選用弧形銜接以提高數(shù)控刀片抗壓強(qiáng)度。加工鈦金屬要常常刃磨數(shù)控刀片以保障其刃形銳利、銑面暢順。
(3)適合的鉆削主要參數(shù)。明確鉆削主要參數(shù)可參照一下計(jì)劃方案:較低的切削用量――切削速度過高造成鉆削溫度大幅度上升;適度的切削速度――進(jìn)給量愈大鉆削溫度高,切削速度小則刃口因在硬底化層中鉆削時(shí)間長而損壞加速;比較大的鉆削深層――尖刀翻過鈦金屬表層的硬底化層鉆削能提升數(shù)控刀片使用壽命。
(4)加工中金屬切削液總流量和工作壓力要大,對加工地區(qū)要充足持續(xù)的制冷以減少鉆削溫度。
(5)采用數(shù)控車床務(wù)必自始至終留意提升可靠性以防止震動發(fā)展趨勢。震動會導(dǎo)致刃口崩碎、刀頭毀壞的結(jié)果。與此同時(shí),加工鈦金屬加工工藝系統(tǒng)軟件剛度好些以確保切割時(shí)選用很大的鉆削深層,但鈦金屬加工回彈力大,夾持力比較大會加重產(chǎn)品工件形變,故精加工時(shí)可以考慮到應(yīng)用組裝工裝夾具等輔助支撐點(diǎn)以達(dá)到加工工藝系統(tǒng)軟件彎曲剛度規(guī)定。
(6)切削方法一般選用銑面。鈦金屬加工中逆銑導(dǎo)致的車刀粘屑和崩刃要比順銑造成的車刀損壞比較嚴(yán)重得多。
(7)切削普遍的問題是粘屑導(dǎo)致沙輪片阻塞及其零件表層燙傷。故切削時(shí)須選用磨砂顆粒銳利、強(qiáng)度高、傳熱性好的綠碳化硅沙輪片;依據(jù)被加工表層光滑度的不一樣砂輪粒度可選用 F36~F80;沙輪片強(qiáng)度應(yīng)過軟,用于降低磨砂顆粒與磨屑的黏附,減少切削熱;磨削切削速度要小、速率稍低,乳化油充裕。
(8)鈦金屬打孔時(shí)必須對規(guī)范麻花鉆開展刃磨以降低燒刀和麻花鉆斷裂狀況。刃磨方式:適度擴(kuò)大夾角、減少鉆削位置偏角、擴(kuò)大鉆削位置前角,圓柱體刃倒光潔度數(shù)翻番。加工中應(yīng)提升進(jìn)刀頻次,麻花鉆不可在孔內(nèi)滯留,立即清理切削,一定量的乳化油制冷,留意觀查麻花鉆變鈍應(yīng)立即清理切削,一定量的乳化油制冷,留意觀查麻花鉆變鈍應(yīng)立即拆換刃磨。
(9)鈦金屬鏜孔也要對規(guī)范絞刀開展改革:鉸刃口帶總寬應(yīng)低于0.15mm,鉆削位置與校正位置宜弧形銜接,防止出現(xiàn)尖點(diǎn)。鏜孔時(shí)可選用組絞刀多次鉸削,每一次提升絞刀直徑0.1mm下列,機(jī)床主軸轉(zhuǎn)速比宜偏慢,退刀時(shí)不泊車。用這類方式鏜孔能做到較高的光滑度規(guī)定。
(10)攻外螺紋是鈦金屬加工中更為艱難的一環(huán),因扭距過大,銑刀刀齒迅速便會損壞,已加工位置的回彈力乃至能使銑刀斷裂在孔內(nèi)。采用一般銑刀加工時(shí)要依據(jù)孔徑尺寸適度降低其齒數(shù)以擴(kuò)大容屑室內(nèi)空間,在校正齒上空出0.15mm總寬的刃帶后需將后角擴(kuò)大至30°上下,除去1/2~1/3齒背,校正齒保存3扣后擴(kuò)大倒光潔度數(shù)。提議采用跳牙銑刀能合理有效的降低數(shù)控刀片和產(chǎn)品觸碰總面積,加工實(shí)際效果亦不錯(cuò)。
加工常見問題
(1)數(shù)控刀片勤刃磨、維持銳利,以保證其加工全過程中造成盡量少的鉆削熱。
(2)機(jī)器設(shè)備、刀、工、工裝夾具應(yīng)維持干凈整潔,切削立即消除。
(3)應(yīng)用難燃或阻燃的專用工具遷移鈦屑。將解決掉的碎渣儲放在沒有易燃器皿中遮蓋好。
(4)實(shí)際操作清理過的鈦金屬零件需戴整潔的膠手套,防止之后導(dǎo)致氧化鈉晶間腐蝕。
(5)鉆削范圍有防火安全設(shè)備。
(6)少量鉆削時(shí),割下的鈦屑一旦著火,聯(lián)軸器數(shù)控機(jī)床加工可以用干粉滅火劑或沙質(zhì)土、干砂澆滅。
結(jié)語
與其它大部分金屬材質(zhì)對比,鈦金屬加工不但規(guī)定更高一些,并且限定大量??墒?,假如恰當(dāng)應(yīng)用適度的數(shù)控刀片,并依照其加工規(guī)定將數(shù)控車床和配備提升到最好情況,一樣可以得到比較滿意的鈦金屬加工實(shí)際效果。
以上就是鑫創(chuàng)盟對 鈦合金零件加工工藝方法分析的介紹,如有問題可隨時(shí)咨詢客服,歡迎致電合作。
以上是《鈦材的加工工藝方法分析》的介紹,原文鏈接:http://sprig-and-sprout.com/cncthjjg/1816.html